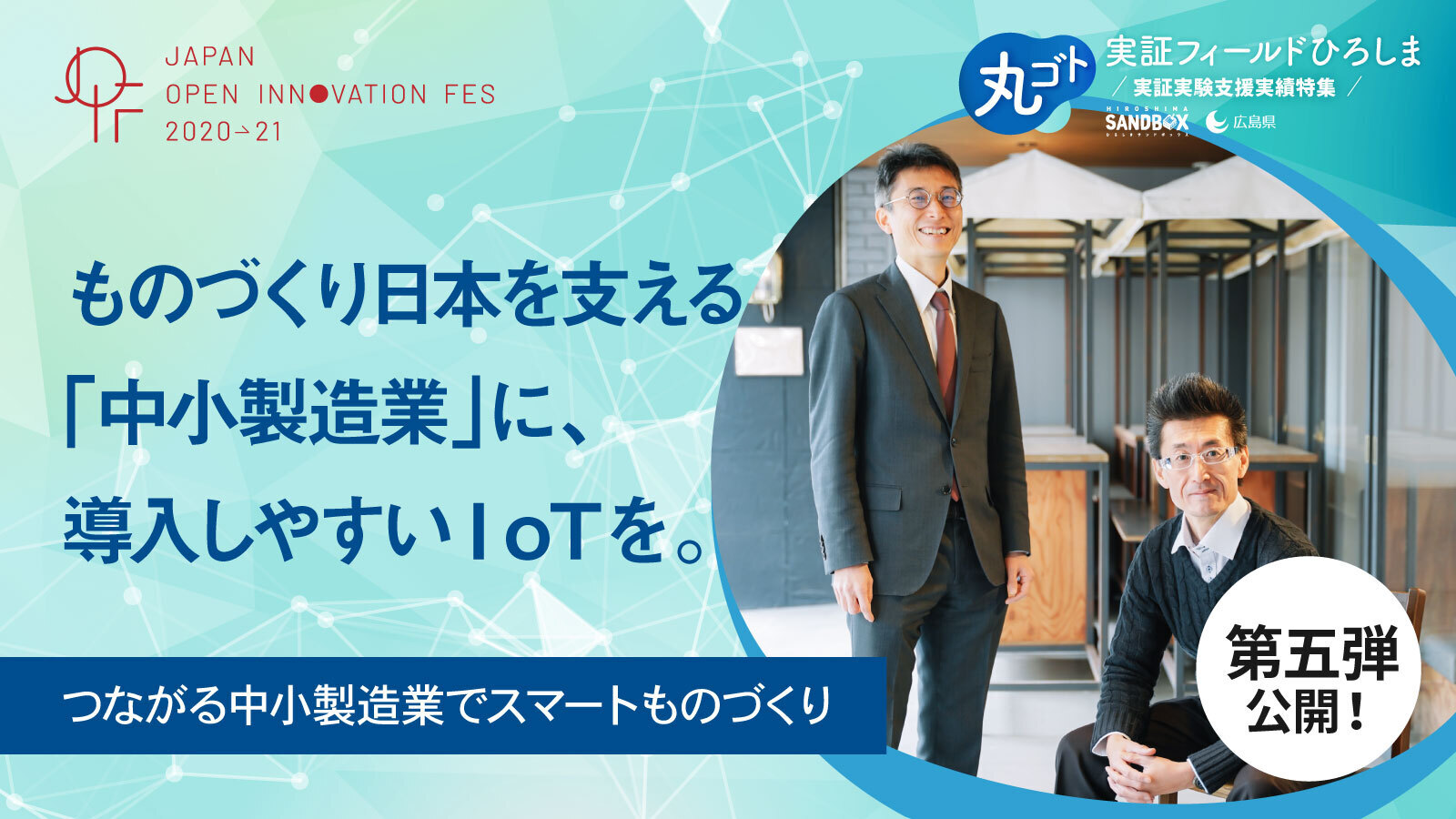
”スマートものづくり”で、中小製造業支援に挑むプロジェクト―「ひろしまサンドボックス」を軸に産学官による9つの実証実験を随時公開中
あらゆるものをインターネットでつなぐIoTは、製造業の現場を大きく変えている。生産性や品質の向上を実現する「スマート工場」に取り組む企業も多い。しかしそれは多くの場合、潤沢な資金やIT人材を擁する大企業に限った話だ。ものづくりを支える中小製造業では、ITの導入=DXが進んでいないことがほとんどだ。予算の問題も大きいが、人や時間の問題もある。大抵の中小企業では、IT専任の担当者はおらず、社長が様々な業務の合間を縫って情報収集をしているからだ。
広島県中小企業診断協会のニューロビジネス研究会では、以前から中小企業でも導入しやすいIoTシステムが開発できないか、議論を進めていた。その折に、ひろしまサンドボックスが立ち上がったのだ。
そこで、ものづくり県・広島を支える中小製造業、そして地元に根差したIT企業であるデジタルソリューションが中心となり、実証実験プロジェクトはスタートした。工場稼働率の見える化、そしてAIによる故障予知や生産工程の最適化に取り組んでいる。リアルなものづくりの現場では、センサーの取り付け1つも苦労の連続だったという。
ひろしまサンドボックスによる「実証実験支援実績特集」の記事第五弾は、”つながる中小製造業でスマートものづくり”にフォーカス。多くの苦難を乗り越えて得たプロジェクトの成果などについて、デジタルソリューションの高下氏、橋詰氏に聞いた。また、本実証事業の中でのひろしまサンドボックスによる様々な支援内容についてもお届けしていく。
▲特設LPにて、「ひろしまサンドボックス」を軸に産学官による9つの実証実験を随時公開!
<取材対象者>
▲デジタルソリューション株式会社 流体解析部/ソフトウェア開発部 部長 高下和浩 氏
▲デジタルソリューション株式会社 ソフトウェア開発部 マネージャー 橋詰公太 氏
IT導入が進まない中小製造業を、なんとか支援したい
――まずは、どのような課題感でコンソーシアムを組成したのか、その背景を聞かせてください。
高下氏 : 始まりは、広島県中小企業診断協会のニューロビジネス研究会からでした。広島県の中小企業の経営者や我々地元のIT企業によって組成された研究会で、AIの普及や活用について模索をしていたのです。
その中で、「中小企業も生産性を向上させなければ、生き残っていくことはできない。しかし、大企業のようにAIやIoTを活用することも難しい」という課題を伺っていました。事実、中小企業にはAI・IoT専任の人材を雇用する余裕はなく、社長が自ら情報を収集するしかない状況でした。
また、当然ながら大企業のようにAI・IoT導入に巨額の資金を投じる余裕もありませんから、非常に苦慮していらっしゃいました。そこで、私たちも地元の中小企業として何かお手伝いができないかと考えていたのです。
ちょうどその頃、ひろしまサンドボックスが立ち上がりました。AI・IoT実証プラットフォーム事業ということで、まさにこの場を活用して様々なトライアルをすることで、中小企業の生産性を向上できるようなAI・IoTシステムを構築したいと考え、ニューロビジネス研究会のメンバーを母体として、参画を決めました。
――コンソーシアムメンバーの中小製造業は、どういった領域の企業が多いのでしょうか。
橋詰氏 : コンソーシアムの中では、自動車関係を中心とした機械加工、特に量産ではなく試作の企業が多いです。試作は少量多品種で、毎回異なるものを作らなければならないため、生産性の向上には特に課題を抱えています。
――地元中小製造業の他に、近畿大学やアプストウェブがコンソーシアムメンバーに加わっていらっしゃいますね。それぞれ、どのような役割を担っているのでしょうか。
高下氏 : 自動車部品の機械加工の工程効率化のためにAI・IoTを活用したいと考えていました。そこで、工程最適化の専門家である近畿大学の谷崎先生に入っていただき、最新のアルゴリズム情報を伺いながらサポートをしていただきました。アプストウェブさんは、情報連携ツールのシステム開発に力を貸していただきました。
【事業内容の概略図】
▲コンソーシアムの構成および、事業の概略。ひろしまサンドボックスがハブとなり、多くの中小製造業が参画している点が特徴的だ。
IoTで工場稼働率を見える化、現場に即した課題に取り組む
――続いて、実証実験をどのように進めていったのか、聞かせていただけますでしょうか。
橋詰氏 : まずは、コンソーシアムメンバーである中小製造業の社長に、どのような困りごとがあるのかヒアリングを行いました。すると、私たちが想定していない課題があることが分かったのです。続いて、その課題を解決するためのシステムを組んで、どのように中小企業にとって使いやすいものにしていくのか、試行錯誤していきました。
――当初想定していた課題とは?
橋詰氏 : 私たちが当初想定していたのは、受発注段階でのシステムを連携して効率化できないかということでした。しかし話を聞いてみると、そこは既に各社システムを導入していて、それらを連携するのは非常にハードルが高かったのです。それよりも、実際に製造現場で本当に困っていることにフォーカスすべきだと考えました。
――具体的に、どのようなことに取り組む計画を立てたのですか。
橋詰氏 : ひとつが、IoTデバイスを使った工場稼働率の見える化です。工場の機械がどの程度稼働しているのか、何となく分かっているつもりですが、実は見えていないという課題がありました。そこで、1つひとつの機器に、センサーやIoTデバイスを取り付けて、稼働率を可視化できるように取り組んだのです。
また、工場には共有の工具や部品があるのですが、管理が徹底されておらず、しばしば行方が分からなくなるそうです。その度に1日30分ほどの時間を費やして探しているということですが、それが非効率だということで、バーコードを取り付けて管理するシステムをつくりました。さらには、機械の故障や異常を検知するシステムや、生産工程の最適化など、現場の課題に沿った計画をしていました。
――中小企業にも取り入れやすいよう、コストを抑えるということも大きな命題だったかと思いますが、そこはどうクリアしたのでしょうか。
橋詰氏 : まず、とにかく安価な機材、センサーを使っていることです。そして、クラウドの仕組みを工夫しました。本来ならIoTのクラウドシステムを使うと、月額10万円以上かかります。しかしそれは、中小企業が負担できる金額ではありません。そこで、自社で汎用のクラウドシステムを使って構築することで、費用を大幅に抑えました。
工場で働く人の反発を乗り越えて、見えた景色
――現場で実証実験を進める中では、様々な苦労があったかと思います。
橋詰氏 : そうですね、私たちは製造業にはあまり精通していなかったため、IoTデバイスを機械に取り付けるだけでも一苦労でした。実際に取り付けてみると、油がいっぱい付着して故障してしまったり、取り付けが甘くてすぐに外れてしまったり。そういったトラブルが絶えませんでした。
試行錯誤の末、現在は改良を加えて、それなりの形にはなっています。ひろしまサンドボックスで、トライアンドエラーができたからこその結果ですね。
高下氏 : はじめは機械の稼働状況をWebカメラで検出しようとしていたのですが、途中で止まってしまったり、周りの環境が映り込んで誤検知されてしまったりして、あまりうまくいきませんでした。
そこで最終的にはパトライトの信号の色で稼働状況をみるようにしました。色々と失敗を繰り返して、最終的に問題なくデータ収集する仕組みが整いましたね。
――工場で働く現場の方には、スムーズに受け入れられたのでしょうか。
橋詰氏 : コンソーシアムの社長に聞いたところによると、導入時に現場から少なからず反発があったようです。生産性の向上が目的なのですが、現場からすると「監視されるのではないか」「もっと働けと言われるのではないか」という抵抗感があったのでしょう。
しかし1年くらい取り組みを進める中で、「工場稼働率は7割程度かと思っていたら、実は3割にすぎない」という数字が見えてきました。その結果を見て、「現場で自分たちはたくさん働いているのに、稼働率が低い。これは何かがおかしい」という声が上がるようになったそうです。
それから、「生産効率を上げるには、何をすればいいのか」について、実際の数字を見ながら議論がされるようになりました。現場から声が上がるようになったことは、大きな進歩です。
――なるほど、実際にデータを取得し可視化することによって、生産性向上の良い兆候が見えているのですね。
橋詰氏 : コンソーシアムメンバーの社長さんたちからも、「機器を取り付けたり、実際に測定したデータを見たりするうちに、AIやIoTに対する抵抗感がなくなった」とおっしゃっていただけます。中小企業の製造現場は、目の前の仕事に手一杯で、新しいテクノロジーの導入に取り組みにくい環境です。ひろしまサンドボックスのような実証実験の場があるからこそ、このように色んなことを試すことができるのだと思います。
人、企業、情報を多面的につなぐ、ひろしまサンドボックスのサポート
――「こういう実証実験の場は、ひろしまサンドボックスならでは」という話がありましたが、ひろしまサンドボックスでは、どのようなサポートを受けましたか。
高下氏 : もともと当社がニューロビジネス研究会でつながっていた企業の他に、この取り組みを導入していただける企業を紹介していただきました。また、情報を分析・可視化する上で、新しいBIツールの情報もいただき、非常にありがたいと感じています。
橋詰氏 : 工業技術センターのセミナーや、IoTリーダー育成プロジェクトなど、広島県やひろしま産業振興機構が主催するイベントや展示会などで、私たちのプロジェクトの紹介をしていただきました。そこに来場されていた企業がコンソーシアムメンバーに加わってくださるなど、情報発信に対する手応えを強く感じています。他にも、プロジェクトスタート時に、ものづくり系媒体への記事掲載の支援もありました。
――先ほど、「製造業にあまり精通していない」というお話しもされていらっしゃいましたが、その辺りの知見のサポートは、ひろしまサンドボックスからあったのでしょうか。
橋詰氏 : ものづくり業界に強いPMOの方を紹介していただきました。広島市のコンサルティング会社、みらい株式会社の方です。工場に一緒に行っていただき、改善点を指摘していただきました。さらに、取り組みの進め方やデータ分析の方法など、様々な視点でご提案を賜りました。これは私たちにはできないことであり、コンソーシアムにとって非常に大きな収穫だったと思います。
業界、地域を超え、日本の中小製造業を支える事業へ
――実証実験は最終局面だと思いますが、今後の予定も聞かせてください。
橋詰氏 : これまでコンソーシアムに13社集まっていただきました。このつながりを、今後につなげていきたいと考えています。そこで、実証実験期間終了後も、コンソーシアムを維持していきたいと考えています。
また、実証実験の期間だけでは、手を付けられなかったこともあります。それに、現状のシステムではまだ製品として販売できる品質に達していないため、引き続き改善を加えながら、最終的には事業化を目指していきたいですね。
――手を付けられなかったこととは、具体的にどのようなことでしょうか。
橋詰氏 : IoTデバイスを使った工場稼働率の見える化については、一定の成果が得られたのですが、物品管理、故障予知、工程最適化については道半ばです。物品管理については、システムはできたのですが、道具や部品にバーコードを取り付けるところがうまくいきませんでした。
これも製造現場ならではのことですが、工場の機械は1万回転したり、水をつかったりするため、はがれてしまうのです。今後も工夫を重ねて、なんとかいい方法を見つけていきたいと考えています。
高下氏 : 故障予知や、工程最適化についても、システムはできているのですが、それを導入して検証する企業さんが繁忙期だったり移転をひかえていたりして、取り組みが遅れてしまっています。ただ、このシステムは特に試作系の企業にとっては「喉から手が出るほど欲しい」と言っていただけるものです。そのため、ここで終わるのではなく、今後しっかりと検証をした上で、しっかりとしたシステムに育てていきたいですね。
――他の業界や、地域に展開していくことも見据えていらっしゃいますか。
高下氏 : 広島県では、食品加工業も盛んです。工程最適化や故障予知システムなどは、食品加工業でも必要とされると思いますので、今後導入を進めていきたいと考えています。
また、実はコンソーシアムメンバーには、愛知県の企業や、和歌山県に本社工場がある企業がいらっしゃいます。そういった点では、既に私たちの取り組みは広島県を飛び出していますので、今後も試作系など少量多品種の生産をする企業に対して、展開をしていきたいですね。
――最後に、ひろしまサンドボックスの魅力を改めてお話しください。
高下氏 : ひろしまサンドボックスでは、実証事業の中で様々な支援を受けながら、試行錯誤できます。もし同じことを社内で提案したとしても、「利益は出るのか」という話になるでしょう。まずやってみて、失敗してもそこからスタートする、こんな経験はひろしまサンドボックスがなければ、できなかったことだと思います。
橋詰氏 : 私たちのような中小IT企業には、製造業へのパイプはほぼありませんが、ひろしまサンドボックスを通して、様々な企業を紹介していただきました。他にも、情報収集やツールの紹介、データ連携基盤など、新たなチャレンジのために必要なリソースの提供があります。このような多面的な支援が、ひろしまサンドボックスの魅力です。
※eiicon companyがオンラインで開催する日本最大級の経営層向けオンラインカンファレンス「Japan Open Innovation Fes 2020→21」にて、スペシャルセッション「オープンイノベーション3.0 産官学連携から見えるみらいのカタチ featuringひろしまサンドボックス」を開催[2/26(金)12:30-13:40]。「ひろしまサンドボックス」を牽引する広島県知事・湯﨑氏をはじめ、9つの実証プロジェクトを代表する担当者がそれぞれの成果をプレゼンします。ぜひ、オンラインでご視聴ください。
視聴方法やスケジュールなど詳細はこちらをご覧ください。 https://eiicon.net/about/joif2020-21/
▲スペシャルセッションの詳細はこちら▲
取材後記
ユースケースの話題3年の実証期間がクライマックスを迎える今、成果としては「道半ば」だということだが、コンソーシアムメンバー各社では、データ連携に対する理解がかなり進んだようだ。これこそ、非常に大きな成果ではないだろうか。世の中のデータ連携への気運が高まる今後、プロジェクトで掴んだ手応えをもとに、各社どのような取り組みを進めていくのか、楽しみである。
(編集:眞田幸剛、取材・文:佐藤瑞恵、撮影:古林洋平)