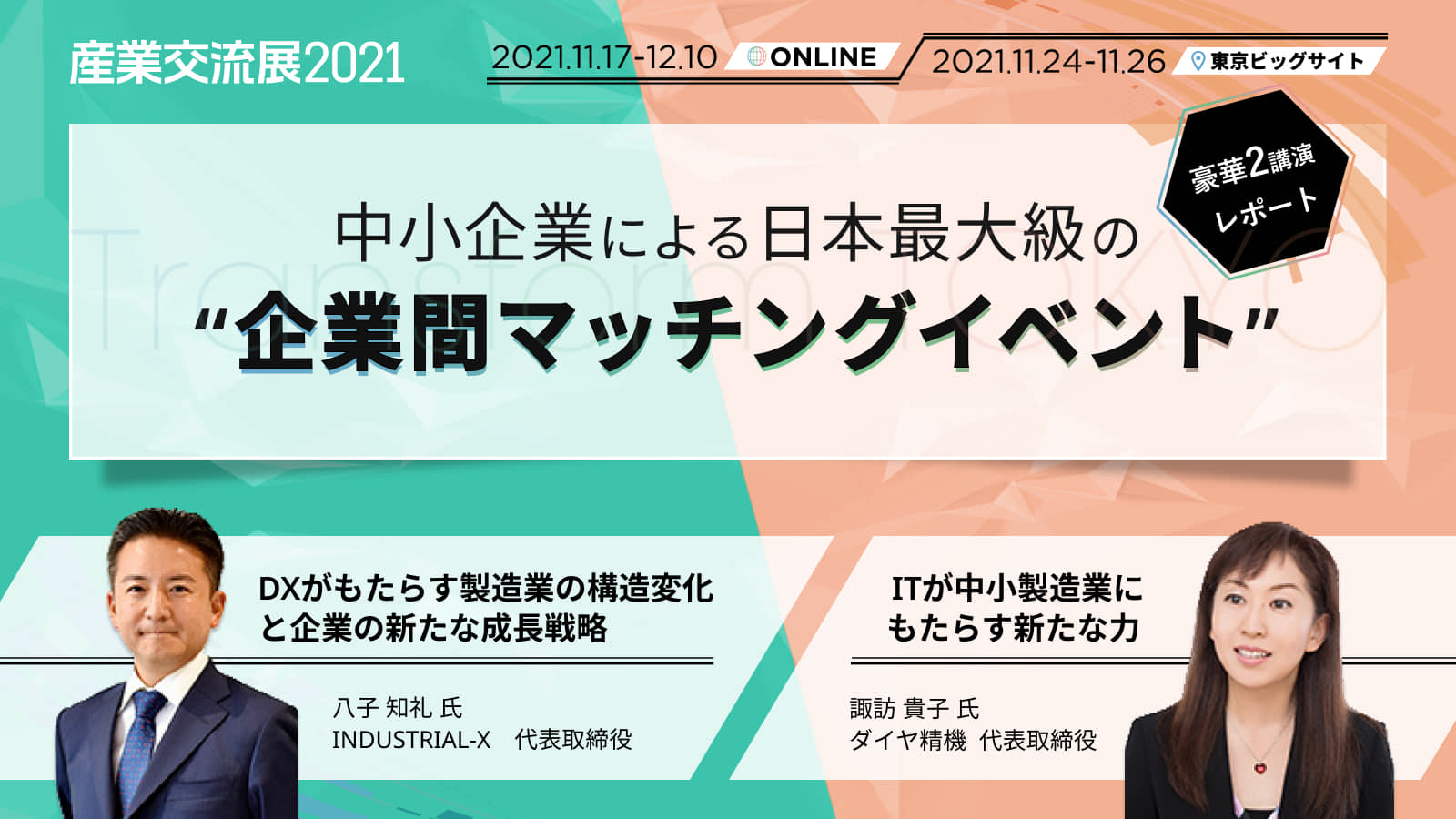
【12/10までオンライン開催中】製造業DXにフォーカスした2講演を詳細レポート!製造業のDX実現のポイントとは?
個性あふれる事業を展開する中小企業の、優れた技術や製品を一堂に展示し、ビジネスチャンスを提供する「産業交流展2021」(東京都や東京商工会議所などが主催)。今年は、東京ビッグサイトによるリアル展示会と、オンライン展示会が並行して開催された(リアル展は11/26に終会)。先日配信した記事でも紹介したように、オンライン展示では、ステージプログラムとして、さまざまな分野の専門家、企業家などによる講演も多数配信されている(12/10まで)。
本記事では、昨今ビジネスシーンで重要視される「デジタルトランスフォーメーション(DX)」にフォーカス。オンライン展示会ステージプログラムのテーマ2、「日本の製造業におけるデジタルトランスフォーメーション」において実施された2本の講演の内容をレポートする。
まず、INDUSTRIAL-X 代表取締役・八子知礼氏の講演では、製造業を対象に、周縁があいまいな「DX」という語を明確に定義し、現在の事業環境下で製造業がDXに取り組む意義を解説。さらに、先進的な取り組みをすでに実施している企業の例にも触れながら、現在進行しつつある製造業のパラダイムシフトについて、仮想化生産、「Factory as a Service」といったコンセプトにもとづき、その実現ステップが提示された。
また、ダイヤ精機株式会社代表取締役諏訪貴子氏の講演では、東京・大田区の小さな町工場の2代目社長として、がんこな職人たちを相手にし、生産プロセス刷新のためのIT導入をいかに進めたのか?さらに、IT化により、どれだけ生産性が向上したのかについて中小企業経営者の現場目線でレポートされた。
講演レポート(1)「DXがもたらす製造業の構造変化と企業の新たな成長戦略」
INDUSTRIAL-X 代表取締役 八子 知礼 氏
1997年松下電工(現パナソニック)入社、製造業の上流から下流までを一通り経験。その後、複数のコンサルティング会社でパートナーまで務めた後、シスコシステムズのビジネスコンサルティング部門のシニアパートナーとして同部門の立ち上げに貢献。ウフルIoTイノベーションセンター所長として様々なエコシステム形成の実績を多数残す。2019年4月にINDUSTRIAL-Xを起業、代表取締役に就任(現職)。2020年10月より広島大学AI・データイノベーション教育研究センターの特任教授就任。広島県産業振興アドバイザー、高知県IoP推進機構理事なども務める。
●デジタルトランスフォーメーション(DX)の本質とは
八子氏の講演では、同氏の考えるデジタルトランスフォーメンション(DX)の本質が定義された。それは、「会社の戦略、ビジネスモデル、組織と風土、業務、プロダクト、顧客との関係性などがデジタルによってすべて新しく生まれ変わること」とされる。
ビジネスモデルやバリューチェーンが新しくなることもそうだが、それにとどまらず、アナログとデジタルをミックスして「デジタルツイン」を作り、会社の姿、ひいてはビジネスの定義そのものを変えていく、そんな「パラダイムシフト」を目指すのがDXの本質である。また、このようなパラダイムシフトとしてのDXを実現しなければ、これからのビジネスでは生き残っていくことが難しくなるという。
●企業のDXへの取り組み調査結果
では現在、日本企業は、本質的な意味でのDXにどの程度取り組めているのだろうか。これに関して、同社が行っているアンケート調査の結果などからの分析が提示された。
まず、DXへの取り組みの狙いをたずねた質問への回答では、「コスト削減」「リードタイム短縮」「品質改善」など、いわゆるQCDの改善を、DXに取り組む狙いとして回答する企業が上位の割合を占めていること、逆に、「顧客獲得」「新規事業拡大」「ビジネスモデル変革」「バリューチェーン改革」など、事業の本質を見直すような狙いでDXに取り組む企業は少数派であることが示された。もちろんQCDの改善は必要なことではあるが、そこにとどまらず、後者のようなビジネス変革を目指すことこそ、DXの本質であり、その点への理解が広まっていないことは、懸念される事態であるという。
ただし、「顧客獲得」「新規事業拡大」の項目は、昨年比で見れば大きく伸びており、この傾向が続けば、少しずつ日本企業でもパラダイムシフトの進展が期待できる。
●DXが道半ばで止まってしまう理由
上記のデータを裏付けるように、八子氏が実際にかかわった企業でも、あるいはそれ以外でも、日本企業では、DXの取り組みを始めても、それが頓挫してしまうことがよく見られるという。それは、部分的にDXを導入しようとした場合、八子氏が「DX・魔のデッドロック」と呼んでいる、次のようなパラドックス状況に陥ってしまうからだという。
デジタル化を進めようとしたとき、たとえば、社内で「設備が古い、システムが古い、投資余力が無い」といった「モノの限界」にぶつかることがある。設備更新などにより、その限界を解決しようとすると、「業務の属人性が強い、人員の配置転換ができない」といった障害にぶつかることがある。では、その「人の限界」を、デジタル化で解消しようとしても、今度は「DXで目指す姿がわからない。そもそも、デジタルというものがわからない。ITリテラシーが低い」といった障害にぶつかる。そういう具合に「デジタル、モノ、人」のどこかを部分的に変えようとしても、他の要素が障壁になってストップしてしまうような状況が、「DX・魔のデッドロック」と呼ばれる。
デッドロック状況に陥らないためには、「デジタル、モノ、人」の三位一体の改革が必要であり、当然ながら、一部門だけではなく、全社的なの取り組みがなされなければならない。
●製造業の大変化と、ものづくりの上流・下流への進出
次に、製造業に焦点を当てて、現在、その最先端で進行中の変化について解説された。IoTの普及、センシング技術の高度化による製造プロセスの可視化は、この5年ほどで非常に進んだ。しかし、そこから後の段階、つまり、可視化された情報をフィードバックし、さらにはそれを活用して制御を自動化していくことについては、成功例はほとんど聞かない。これには、制御の難しさだけではなく、セキュリティの問題もある。
しかし、デジタルによるプロセスの可視化が普及したら、その次には、フィードバックと制御が、必ず大きなビジネス領域になる。「スマイルカーブ」として示されてきた製造工程の前工程(R&D、企画など)と、後工程(サービス)の付加価値が高くなる形、あるいは、「もの売りからサービスへ」というかけ声は、20年以上前からよくいわれていた。だが、実際には、失われた20年、30年といわれる低成長の時代にあって、日本の製造業は、主には、製造工程の最適化や内部改善に注力してきた。
それが、ここに来てようやく大きな変化を見せている。たとえば、MBD(Model Based Development)、MBSE(Model-based Systems Engineering)などの普及により、開発、設計、製造、運用最適化までがデジタルのシミュレーションにより一気通貫で行える状況が作られている。さらに、後でも述べるが、そこで蓄積されたデータを活用してさらに新しいビジネスへの取り組みが可能になる。
●「仮想化」されていく製造プロセス
続いて、製造現場で進むさまざまな変化の事例が示された。たとえば、部品点数が多く、いわゆる「すりあわせ」が欠かせないためにモジュール化が進みにくいといわれてきた自動車業界でも、この2年ほどで、大きな変化が起きている。中国のBYTON、日本のSONY、アメリカのCANOOなどは、いずれも、MBSE、3Dのシミュレーションによるモデルベースの開発設計とエンジニアリングで、組み合わせベースで車を開発している。そのため、EV(電気自動車)をゼロから開発して、わずか2、3年ほどで完成させた。このような短期間の開発は、従来の自動車業界からすると驚異的である。
また、3Dプリンティングサービスビューロー、AM(Additive Manufacturing)、GD(Generative Design)といった手法も、ものづくりを大きく変化させている。3Dプリンタを南米やロシア内陸などに置き、必要な時にデジタル設計データをお送り、そこで3D出力すれば在庫も不要で輸送費もおさえられる。
その3Dプリンタでは、AM(Additive Manufacturing)という、複雑な3次元空間の造形を、削り出しではなく積層形成で作る技術が進歩し、金属加工の3Dプリントで、量産品も製造も可能になっている。これにより、部品点数が激減させることができる。
さらに、その設計には、GD(Generative Design)の技術が用いられる。これは、魚の骨や植物の葉脈などのデータから、それに近い構造を、AIにより自動生成してデザインする仕組み。AIが自動生成した設計データから3Dプリンタで生成すれば、これまで作れなかったものも作れる。
このような現場の変化を背景に、マニュファクチャリングが仮想化していくと、八子氏は考えている。R&Dからサービス提供までのサプライチェーンにおいて、デザイン、設計、製造、品質検査など多くの部分がAI化、自動化され、さらに遠隔操作での3D出力などが可能になることで、製造プロセス全体が「仮想化」されていく。この仮想化という概念は、現時点では八子氏が提示する仮説だが、それに近いトライをしている会社はいくつもあるという。これこそ、DXによるパラダイム転換である。
●製造業のビジネスモデルも変わっていく
仮想化へと進む製造現場の変化は、製造業のビジネスも変えていく。これまで、製造業のキャッシュポイントは、主には、製造、販売、サービスの時点であった。ところが、サプライチェーン全体がデジタル管理されるようになると、設計、調達、製造、販売、物流、サービス、さらには、プロセス最適化や、そのノウハウ化など、キャッシュポイントが大幅に増加する。
たとえば、デジタル化は共同調達を容易にし、調達金額が下がればマージンが生める。あるいは、製造工程の稼働時間をマッチングプラットフォームで販売したり、そのマッチングプラットフォームの利用そのものに課金したりするといったことも可能になる。IoTの仕組みを構築したら、その仕組みを外販する。その仕組みを使って、稼働保証や品質保証といったサービスを販売することもできるだろう。
また、利用されるIoTで実際にデータが集積されれば、それを分析加工すれば、さまざまなノウハウがたまる。そのノウハウをサブスクで提供することもできる。このように、従来の製造業の枠では考えられなかった、デジタル領域でのキャッシュポイントが設定できるようになる。
さらに、これまで、生産されるモノは、時間の経過によって陳腐化するために、モノの価値は時間が経つにつれて低減せざるをえなかった。しかし、データを活用したサービスを付加すれば、むしろ時間が経てば経つほどデータが集積し付加価値が高まる。このようにして、以前からいわれてきた、「ものづくりのサービスへのシフト」が、本当の意味で具体的に実現できるようになる。
●Factory as a Serviceを目指すステップ「SFoF:Smart Factory of the Future」
最後に、これまでの議論を踏まえた上で、今後の製造業が目指すべきDXのプロセスとして、八子氏が提唱している、「SFoF:Smart Factory of the Future」というモデルの説明がなされた。
これは、製造業のDXを、最初期の「レベル1:IoTによるデータ収集」から、「レベル2:可視化」「レベル3:遠隔化」「レベル4:予期化」「レベル5:自動化」「レベル6:プラットフォーム化」を経て、「レベル7:FaaS化(Factory as a Service、工場全体でのオンデマンド製造サービス化)」へ至る進行プロセスとしてとらえるフレームワークである。
今後、本質的なDXを進めていくには、いま自社がどこのレベルにあって、どこのレベルを目指すのかを真剣に考えることが必要だとされた。その上で、DXサポートツールとして、同社が提供している「Resource Cloud」にも触れられた。Resource Cloudは、DX進行に向けて企業が直面するさまざまな課題の解決手段を、包括的にサービスとして提供するオンライン会員制サービスだ。同サービスの活用により、短期でDXが進展させることに成功した企業の例が紹介され、講演が締めくくられた。
講演レポート(2)ITが中小製造業にもたらす新たな力
ダイヤ精機 代表取締役 諏訪 貴子 氏
1971年東京都大田区生まれ 成蹊大学工学部卒業後、ユニシアジェックス(現・日立Astemo)でエンジニアとして働く。32歳(2004年)で父の逝去に伴い専業主婦から急遽ダイヤ精機社長に就任。IT化を含む3年の改革を断行し、新しい社風を構築した。育児と経営を両立させる女性経営者として活躍中。日経BP社Woman of year 2013 大賞を受賞。ニュースZEROや日曜討論等のメディアに多数出演し、中小企業の現状を伝えている。 2017年には著書「町工場の娘」がNHKでドラマ化された。
●典型的な日本の町工場
東京・大田区で創業50年余を数えるダイヤ精機株式会社は、大手企業から受注した製品を製造する典型的な中小町工場だ。現社長の諏訪貴子氏は、2004年、父親である先代社長の急逝を受けて跡を継ぎ、社長に就任した。専業主婦だった諏訪氏が、突然社長を引き受け奮闘しながら中小企業を盛り立てた様子は、2015年に『町工場の娘』(日経BP)として書籍化され、さらに、2017年には書籍をもとにNHKでテレビドラマ化もされている。
諏訪氏は、同社の中心業務は、「鉄の磨き上げ」だという。具体的には、同社製品は、「ゲージ」と「金型」である。前者は1ミクロン単位の精度が求められ、後者は10~100ミクロン単位の精度となる。いずれも少数の多能工が熟練された技術で製造している。1ミクロン単位の精度で鉄を磨き上げる技術は、日本の中小企業が持つ強みであり、これを後世に残していくことが自らの使命と考えているという。
諏訪氏が社長に就任した時、諏訪氏より歳下の社員は3人しかおらず、50代、60代の社員が中心で逆ピラミッド型の年齢構成になっていた。若手が増えなければ技能の伝承もできないので、2007年から、人材確保・育成に注力しはじめる。そして、10年以上の時間をかけて取り組み、現在では20代、30代の社員が過半数のピラミッド型構成になった。
ただし、ものづくりにおいては、熟練の経験がものをいう部分がどうしてもあるので、社員が若年化したことで、実のところ、生産性が落ちてしまった。しかし諏訪氏は、「課題があるということは、解決すれば成長できるということ」といい、その解決手段の1つとしてIT導入を活用している。
●社長就任後の社内改革
諏訪氏は、社長就任後、3年をかけて社内改革を行った。1年目は「意識改革」をテーマとして、挨拶の仕方といった基礎の基礎から、徹底させ社内の基盤を作った。また、組織改革にも着手。意見集約型、ボトムアップ組織とするため、組織の縦の階層を圧縮して、その代わりに複数のサークルを置いて、サークルのリーダーから意見を聴取してトップが決断する組織とした。
2年目は「チャレンジ」をテーマとして、まず、老朽化した生産設備を新しい設備に入れ替え、生産管理システムを全面変更した。また、過去40年の資料をもとに、SWOT分析を実施。諏訪氏は、自社の強みを「技術力」だと判断した。しかし、それをある人に見てもらったところ「顧客の視点がない」と指摘される。そこですぐに顧客に自社への発注理由をたずねたところ、「対応力」の高さが評価されていることがわかった。諏訪氏には、それは意外だったが、顧客から評価されている面を伸ばそうと考えて、生産管理システムを全面変更することとした。
3年目は「維持継続、発展」がテーマとされた。社内改革に取り組みをはじめて、1、2年目はモチベーションが高いので、それなりに進むが、それをさらに長期間維持することが難しい。そこで、各業務の棚卸と、ムダを排除した業務の標準化を実施。また、改善スキルの向上を目標に社内QC活動を活発化、熟練職人と若手社員とのパートナー業務を随時取り入れて技能承継をマンツーマンで教育するなどの施策を実施した。
●生産管理システム選びと、その導入
諏訪氏は、顧客が評価する対応力の高さをさらに伸ばすため、生産管理情報を一元化して、納期短縮を図るべく、生産管理システムを再構築することした。
まず従来の管理システムの問題点を洗いだしたが、課題は「製造の進捗の把握・管理ができていないこと」だと考えられた。そこで、受注から納品までの生産情報を一元管理するために、バーコードを用いて進捗管理、原価管理ができるシステムを導入した。システム導入にあたっては、多くの展示会に足を運び、求める機能を持つソフトを探す。次に、3社に絞って社内プレゼンしてもらう。さらに、2社に社内データを渡して、社内で社員の前でデモをしてもらい、最終的に1社に決定するというプロセスを踏んだ。
また、社内での導入から稼働までのプロセスは「システム検討」「プレゼン及び社内展開」「教育、マスター登録」「テスト稼働」で、約1年間かかった。初期においては、諏訪氏が社内でプレゼンして、社員との質疑応答を何度も繰り返したことがポイントであった。なぜなら、職人は、システムをなんのために使うのかが納得できなければ使ってくれないためだ。しかし、役に立つと納得できれば、とことん使ってくれる。
職人は、最初はパソコンの使い方を知らない人も多く、電源を入れ方、ダブルクリックの仕方といったレベルから始めた。それでも、システム導入後のテスト稼働開始から実際の運用まで、半年か1年くらいかかるだろうと見積もっていたが、実際には3か月で本格運用ができたという。導入後の効果としては、生産設備更新のようにすぐに目に見える効果は上がらない。しかし、通年を通して見たところ営業利益率、経常利益率などの数値が向上しており、確実な費用対効果があった。
●2020年の新システムの導入
旧生産管理システムの導入から15年以上経過し、バーコードリーダーの故障などもあったため、昨年に新システムを導入した。今回の導入目標は、進捗管理のレスポンス向上、生産計画の明確化などであった。
旧システムの問題点は、POPのバーコードリーダーに寿命がきたこと、その買い換えがかさむこと、現場のPOP操作の時間、事務作業の負荷などであった。そして、それらを解決するため、POPではないこと、いままでは含まれていなかった見積もり段階からのデータ連係ができること、現場操作がより簡便であることなどを求める要素として新システムを探した。新しい生産管理システムでは、見積り段階からのデータ連動、ハンディターミナルに替わってPADでの管理、また、本社と工場をLANで繋いでリアルタイムでの情報共有などが可能になった。
●クラウド型コミュニケーションツール導入による情報共有の効果
生産管理システムの置き換えと並行して、クラウド型のコミュニケーションツールも導入した。先に述べたように、2007年からの約15年間で、社員の年齢構成をピラミッド型へ転換することに成功したが、その一方で生産性が低下してしまった。機械の稼働中の業務効率は、熟練職人でも若手でもさほど差は無いものの、段取時間などには、どうしても経験の差が出てしまうためである。そこで、機械稼働率を向上させるための施策に取り組むこととした。
その1つが、いわゆる「5S」の徹底化である。そしてもう1つが、会議や、電話、営業担当者との確認などを減らすための情報管理・共有である。そのために、クラウド型のコミュニケーションツールを活用することとした。まだ受注していない見積り段階の情報について、以前は、製造部門は関知できなかった。しかし、稼働率を向上させて生産性を高めるためには、見積り段階も含めて、社内の全部門の情報を、全員が共有する必要がある。
そこで、すべての部門の情報をあげて、全部門で双方向の情報管理をするために、コミュニケーションツールを活用することとしたのだ。その導入により、①社内での情報の行き違いがない、②社内外のどこにいても図面管理ができる、③部門を超えたコミュニケーションがとりやすくなる、④チャットや掲示板機能で、連絡時間のムダがなくなる、⑤設計の負荷や進捗が把握でき、負荷が平準化される、などの大きな効果が得られた。さらに、部門によっては在宅勤務も可能になった。
これらの効果により、新システムの導入前後を比べると、営業利益率は実に8倍にも増加するという、顕著な結果が得られた。
●中小企業のデジタル化の進め方と注意点
最後に、中小企業がデジタル化、IT導入を行う際に意識すべき点や、進め方のポイントが説明された。諏訪氏がかつて実施した社内改革でも、1年目は意識改革を徹底し、2年目以後に生産管理システムを導入した。このように、まず組織としての、改革を進める体制を構築してからIT化に進むことが成功につながる。
経産省では、目指したいデジタル化のレベルとして「デジタイゼーション」「デジタライゼーション」「デジタルトランスフォーメーション(DX)」の3段階を示している。また、その中に「守り」と「攻め」を設定している。それに即して、現状で自社がどの段階にあって、次になにを目指すのかを確認することも必要ではある。しかしそれだけではなく、顧客目線で考えたときに、どのようにすればより良く製品を届けることができるのか、そのために排除すべき自社の問題やムダがどこにあるのかを把握し、そのためITが使えないのかを検討するのがよい。
具体的なプロセスとしては、①目標の設定(なにがしたいのか)→②課題の抽出(なにができていない)→③現状把握→④対策検討(組織や業務フロー見直しも含む)と、進めていく。また、進める際に注意すべきポイントとしては、社員の意見を取り入れて、全員意思で取り組むこと、特にパッケージソフトを導入する場合には、最初からシステムのすべての機能を使おうとは思わないこと、また、まず3週間は続けさせて習慣化させること、などが挙げられた。
締めくくりとして、自社の経験からも、デジタルを導入してIT化をすれば、必ず生産性は上がる。ITコーディネータなど国の支援制度もあるので、うまく活用して、ぜひ生産性を向上させてほしいと述べられた。
取材後記
DXによる大きなパラダイムシフトの方向を俯瞰する八子氏の講演と、中小企業の現場でのIT導入のポイントや進め方を教えてくれる諏訪氏。両者の講演をあわせてみることで、「日本の製造業におけるデジタルトランスフォーメーション」というテーマを、鳥の目、虫の目、魚の目で見ることができるのではないだろうか。
今回の産業交流展・オンライン展のステージプログラムでは、他にも多くの魅力的な講演プログラムが配信されている。出展各企業の展示配信とあわせて、自社のビジネスに役立つ情報が得られるチャンスだ。12/10までの開催期間中に、一度アクセスしてみてはいかがだろうか。
※「産業交流展2021」の詳細についてはこちらをご覧ください。
(編集:眞田幸剛、取材・文:椎原よしき)